Understanding Plastic Injection Molding Manufacturers
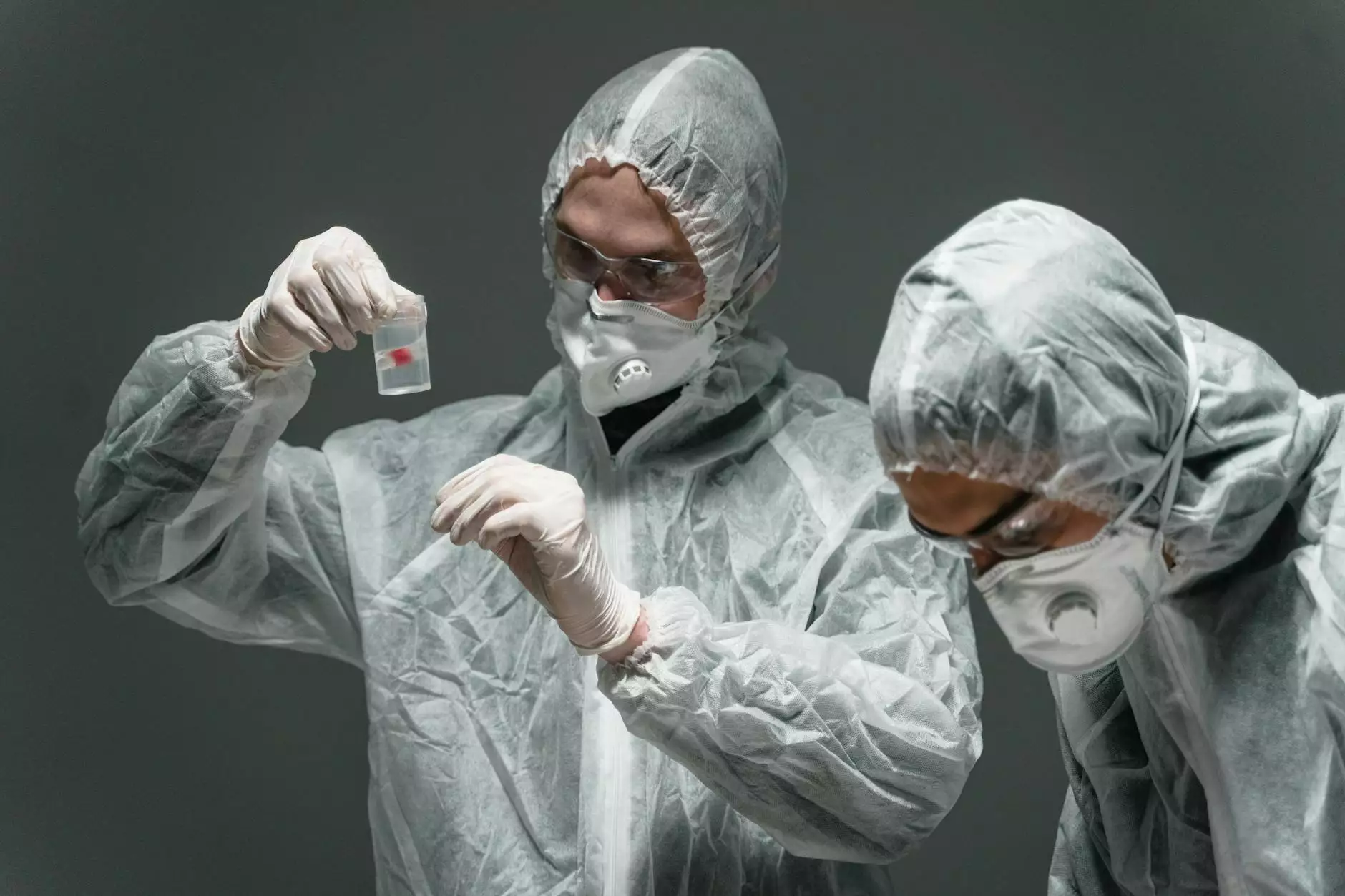
Plastic injection molding manufacturers are at the forefront of a transformational process that shapes the modern manufacturing landscape. This technique, which involves injecting molten plastic into a mold to create a desired shape, is essential for producing a vast array of plastic products used in numerous industries. In this extensive article, we will delve deep into the processes, advantages, applications, and the future of plastic injection molding manufacturing.
What is Plastic Injection Molding?
At its core, plastic injection molding is a manufacturing process that produces parts by injecting molten materials into a mold. This process is highly efficient and can produce large volumes of parts at a relatively low cost. The typical steps in plastic injection molding include:
- Material Selection: Choosing the right thermoplastic resin, such as ABS, polypropylene, or polycarbonate, which influences the properties of the final product.
- Mold Design: Creating a mold that meets the specifications of the desired part, considering aspects such as draft angles and cooling channels.
- Injection: Molten plastic is injected into the mold cavity under high pressure.
- Cooling: The component cools and solidifies in the mold.
- Ejection: The mold opens, and the finished part is ejected.
The Role of Plastic Injection Molding Manufacturers
Plastic injection molding manufacturers play a crucial role in the production process. They are responsible for the following:
- Designing and fabricating high-quality molds.
- Choosing appropriate materials for a variety of applications.
- Managing the production process to ensure efficiency and quality control.
- Meeting specific industry regulations and standards.
Advantages of Using Plastic Injection Molding
Choosing plastic injection molding over other manufacturing processes offers several advantages, including:
- High Efficiency and Speed: Once a mold is created, manufacturers can produce thousands of identical parts rapidly.
- Complex Geometries: The process allows for intricate designs that would be difficult or impossible to create through other methods.
- Material Versatility: Various thermoplastics can be used, providing options for strength, flexibility, and resistance to heat or chemicals.
- Low Waste and Cost-Effectiveness: The process minimizes waste, allowing manufacturers to produce more parts from less material.
Applications of Plastic Injection Molding
The applications of plastic injection molding are vast and varied, making it a go-to choice for many industries, including:
1. Automotive Industry
In the automotive sector, plastic injection molding is utilized for numerous components such as dashboard panels, door handles, and polymer-based structural parts. Manufacturers can produce lightweight, yet durable parts that aid in fuel efficiency and vehicle safety.
2. Consumer Products
From kitchenware to electronics, the consumer products industry relies heavily on plastic injection molding manufacturers for creating everyday items. This includes products like containers, toys, and appliances that require a high degree of customization and cost-effectiveness.
3. Medical Devices
The medical industry demands precision and compliance with stringent regulations. Plastic injection molding is crucial for producing sterile and intricate components in devices such as syringes, surgical tools, and diagnostic equipment.
4. Industrial Applications
Industrial sectors employ injection-molded plastics for various functions, including machinery housings, electrical casings, and specialized components that need to withstand harsh environments.
The Future of Plastic Injection Molding
The future of plastic injection molding looks promising, with advancements in technology and materials. Some key trends include:
- 3D Printing Integration: The combination of 3D printing with traditional injection molding techniques could lead to customized, rapid production processes.
- Recyclable Materials: As sustainability takes precedence, manufacturers are exploring biodegradable and recyclable plastics to meet eco-friendly standards.
- Smart Manufacturing: The integration of IoT and AI technologies in monitoring processes for enhanced efficiency and predictive maintenance.
Choosing the Right Plastic Injection Molding Manufacturer
When selecting a plastic injection molding manufacturer, consider the following factors to ensure you choose the best partner for your needs:
- Experience and Expertise: Look for manufacturers with a proven track record and extensive industry experience.
- Quality Assurance: Ensure they implement stringent quality control measures to meet industry standards.
- Technology and Equipment: Advanced machinery and technology can enhance production efficiency and product quality.
- Customer Support: A reliable manufacturer should offer strong communication and support throughout the process.
Conclusion: Embracing the Potential of Plastic Injection Molding
In conclusion, plastic injection molding manufacturers are indispensable in creating high-quality plastic products across various industries. The flexibility of this manufacturing process makes it essential for businesses looking to innovate and enhance their product offerings. The ongoing evolution of technologies and materials promises an exciting future in this field. By partnering with the right plastic injection molding manufacturer, businesses can leverage their capabilities, reduce costs, and consistently deliver exceptional products. For your injection molding needs, consider exploring more about the offerings at deepmould.net.