Unlocking the Potential of Plastic Molding in Modern Business
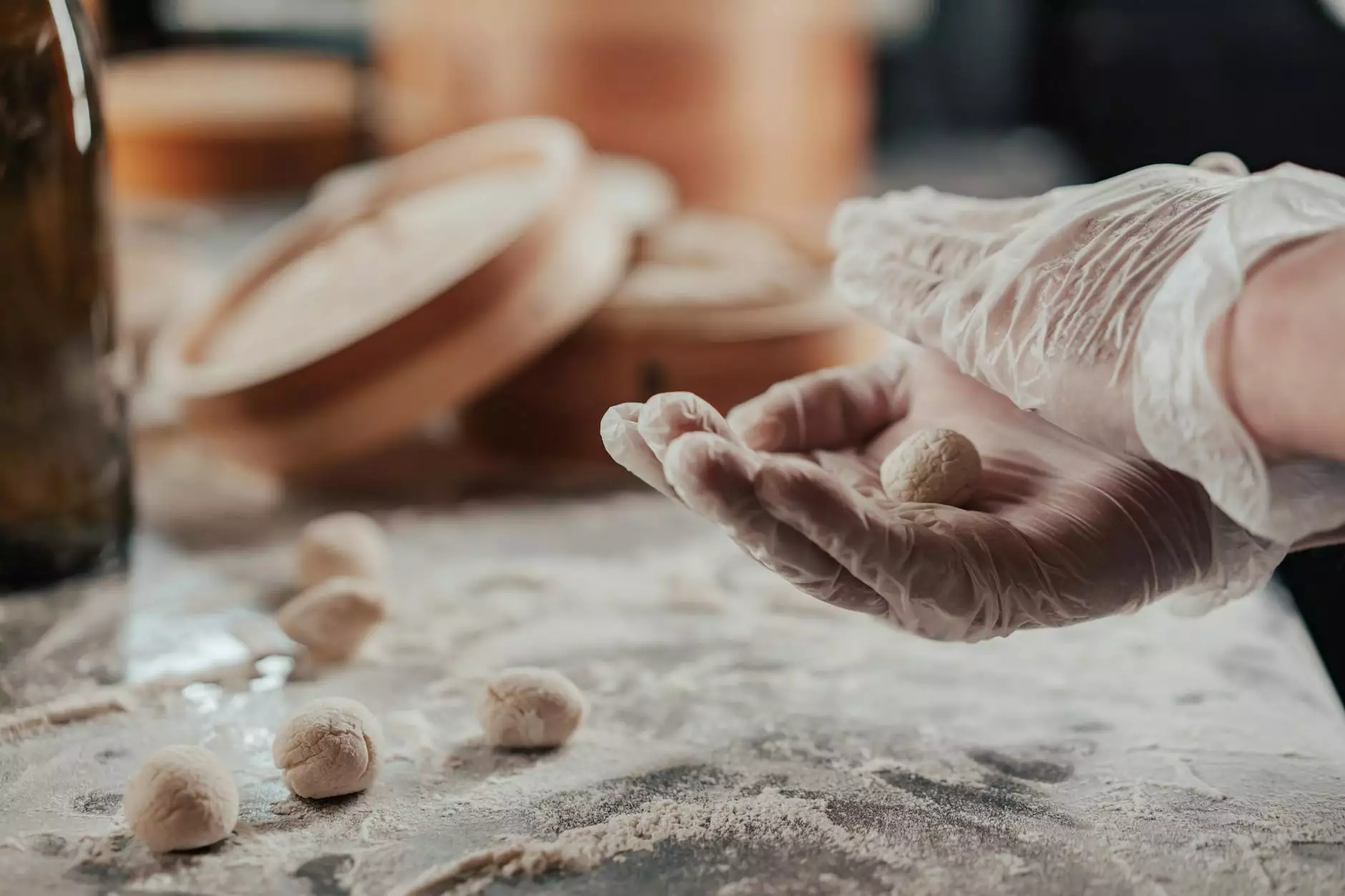
In the fast-evolving landscape of manufacturing, plastic molding has emerged as one of the most revolutionary processes, fundamentally changing the way products are designed and produced. This article serves as a comprehensive overview of the plastic molding industry, exploring its benefits, techniques, applications, and its indispensable role in business growth, particularly for companies like Deep Mould that operate within the sector of metal fabrication.
What is Plastic Molding?
Plastic molding is a manufacturing process that involves the shaping of plastic materials by heating them until they are malleable, then forcing them into a mold. After cooling, the mold is removed to reveal the final product. This method is not just limited to one type; there are various techniques involved, which we will discuss in detail below.
The Major Types of Plastic Molding Techniques
1. Injection Molding
Injection molding is the most widely used plastic molding technique. In this process, plastic granules are heated and then injected into a mold cavity under pressure. This method is highly efficient and capable of producing complex geometries with precise dimensions.
- High production rates
- Ability to use a diverse range of materials
- Tight tolerances
- Minimal waste
2. Blow Molding
Blow molding is primarily used for creating hollow plastic products such as bottles and containers. The process involves inflating hot plastic within a mold using air pressure. This method is particularly beneficial for the beverage industry, where high manufacturing throughput is essential.
3. Rotational Molding
Rotational molding is ideal for creating large, hollow parts. The process involves rotating a heated mold filled with powdered plastic, allowing the material to coat the mold's interior evenly. This technique is cost-effective for low-volume production but produces robust and durable items.
4. Compression Molding
Compression molding is primarily used for thermosetting plastics. It requires placing a preheated plastic material into a mold, which is then closed under pressure. The heat and pressure cause the material to flow and take the shape of the mold. This process is efficient for larger parts and lower-volume needs.
Advantages of Using Plastic Molding in Business
Cost Efficiency
One of the primary advantages of plastic molding is its cost-effectiveness. The ability to mass-produce items quickly and with minimal waste leads to significant savings. Businesses can reduce production expenses and offer more competitively priced products.
Design Flexibility
With plastic molding, manufacturers can produce intricate designs and complex components that would be challenging, if not impossible, with other manufacturing methods. This design flexibility is essential for innovation and product differentiation.
Material Versatility
The variety of plastics available today offers businesses the ability to select materials best suited for their needs, whether they require durability, resistance to chemicals, or lightweight characteristics. This versatility expands the potential applications for businesses in multiple industries.
Quick Prototyping and Production Times
The speed at which plastic molding can turn a concept into a tangible product is remarkable. Businesses can iterate on designs quickly, reducing time to market and staying ahead of competitors. The ability to easily create prototypes allows for rapid testing and adjustments.
Applications of Plastic Molding Across Industries
Plastic molding is integral to a wide range of industries, making it a cornerstone of modern manufacturing.
1. Consumer Products
From household items to toys, plastic molding produces countless consumer products that are integral to daily life.
2. Automotive Industry
The automotive sector heavily relies on plastic molded parts due to their lightweight properties, which help improve fuel efficiency and performance.
3. Medical Devices
In the medical field, precision and reliability are paramount. Plastic molding provides the necessary standards and hygiene, making it useful for producing components like syringes, surgical instruments, and disposable supplies.
4. Electronics
Many electronic products use plastic molded cases and components to protect sensitive parts, enhance durability, and provide aesthetic appeal.
Choosing the Right Plastic Molding Partner
Selecting the right partner for your plastic molding needs can significantly impact your business's success. Here are some key factors to consider:
- Experience: Look for a partner with a proven track record in the industry.
- Technology: Ensure they utilize the latest technology and equipment to produce high-quality products.
- Customization: Your partner should offer tailored solutions to meet your specific needs.
- Quality Control: A robust quality control system is essential to guarantee product reliability.
- Customer Service: Effective communication and support are crucial throughout the production process.
Future Trends in Plastic Molding
As the manufacturing landscape shifts towards sustainability, the field of plastic molding is also evolving. Key trends to watch include:
1. Sustainable Materials
With the increasing focus on sustainability, the use of biodegradable and recycled plastics in molding processes is on the rise. Businesses that adopt these materials will be better positioned to meet consumer demand for eco-friendly products.
2. Advanced Manufacturing Technologies
The integration of technologies such as 3D printing and automation is revolutionizing traditional plastic molding processes, enabling greater efficiency and customization.
3. Emphasis on Lightweight Designs
A continued push for lightweighting in industries, especially automotive and aerospace, drives innovation in plastic molding to optimize strength-to-weight ratios.
Conclusion
In conclusion, plastic molding is a transformative technology that plays a crucial role in modern manufacturing. Its wide array of applications, significant advantages, and opportunities for innovation make it an invaluable asset for businesses looking to thrive in today's competitive environment. Companies like Deep Mould, specializing in metal fabrication, can further enhance their offerings by integrating plastic molding techniques into their production processes, thereby unlocking new markets and increasing profitability.
By staying ahead of trends and focusing on quality and customer needs, businesses can fully leverage the potential of plastic molding to create products that meet the demands of a rapidly changing marketplace. The future of manufacturing is here, and it is plastic!