Understanding LOLER Legislation: Ensuring Safety and Compliance in Your Business
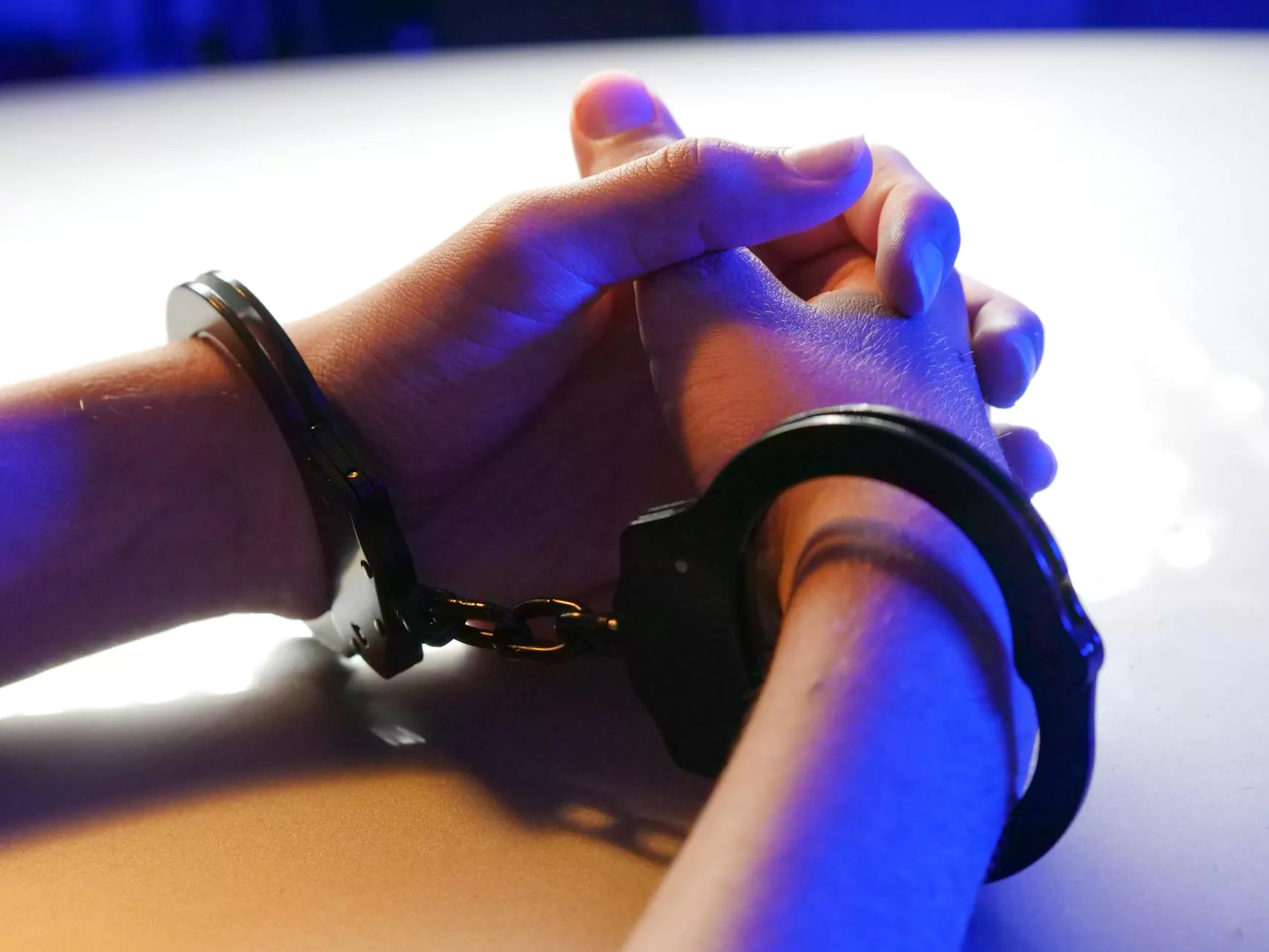
In today's industrial and commercial environment, the significance of safety standards cannot be overstated. One of the fundamental regulations that safeguard workers and operational efficiency is the LOLER legislation. This regulation, formally known as the Lifting Operations and Lifting Equipment Regulations 1998, plays a pivotal role in ensuring that lifting equipment used across various sectors, including Home & Garden, Gardeners, and Pest Control businesses, is maintained, inspected, and operated safely. Understanding LOLER legislation is essential for business owners committed to compliance, safety, and minimizing operational risks.
What is LOLER Legislation? An In-Depth Overview
LOLER legislation is a legal framework introduced by the UK government to regulate all lifting operations and equipment. Its primary purpose is to protect workers from hazards associated with lifting gear, such as cranes, hoists, lifts, slings, and other lifting machinery. The regulation emphasizes proper maintenance, regular inspections, and thorough training to prevent accidents.
Enforced by the Health and Safety Executive (HSE), LOLER requires that:
- All lifting equipment be suitable and safe for use.
- Regular thorough examinations and inspections are carried out by competent persons.
- Proper records of examinations and maintenance are maintained.
- All operators are adequately trained and competent to handle lifting equipment safely.
The Scope of LOLER legislation and Its Relevance to Your Business
The scope of LOLER legislation is extensive, covering a wide range of lifting equipment including:
- Industrial cranes and hoists used in large scale operations.
- Vehicle lifts utilized by mechanics and garages.
- Lifting slings, chains, and lashing equipment for various applications.
- Portable lifting devices and electrical hoists applicable in garden and pest control businesses.
- Any equipment used to lift, lower, or suspend loads in your operations.
For businesses involved in Home & Garden, Gardeners, and Pest Control, compliance with LOLER legislation might seem less obvious but remains critically important. For instance, if you use lifts to access elevated areas, or hoisting equipment in pest control setups, you must adhere to these regulations to ensure safety and legal compliance.
Why is Compliance with LOLER legislation Crucial?
Adherence to LOLER legislation is not just about avoiding legal penalties; it is fundamentally about safeguarding lives and protecting your business reputation. Non-compliance can lead to severe consequences, including:
- Legal action and penalties from regulatory authorities such as the HSE.
- Financial loss due to fines, compensation claims, and operational downtime.
- Injury or fatal accidents that could have been prevented through proper safety measures.
- Damage to business reputation leading to loss of client trust and future opportunities.
Beyond legal and financial reasons, adhering to LOLER principles demonstrates a true commitment to workplace safety, which can improve employee morale and productivity.
Implementing LOLER compliance in Your Business: Step-by-Step Guide
1. Identify All Lifting Equipment
Start with a comprehensive audit of all lifting devices used within your operations. This includes equipment such as forklifts, cranes, hoists, lifts, sling systems, and portable lifting tools. Classify each item based on size, capacity, and usage to determine compliance requirements.
2. Ensure Equipment Suitability and Safety
Verify that all equipment is appropriately rated for your intended loads and environments. Equipment must be designed and maintained to meet safety standards, with manufacturers’ guidelines followed meticulously.
3. Schedule and Conduct Regular Thorough Examinations
LOLER mandates periodic inspections by qualified, independent professionals. These examinations assess the integrity, safety, and proper functioning of the equipment. The frequency of inspections depends on equipment usage but generally follow a minimum schedule of every 6 or 12 months.
4. Maintain Accurate Records
Keep detailed documentation of all inspections, maintenance work, and repairs. These records are vital for demonstrating compliance during audits and for ongoing safety management.
5. Train Your Staff Appropriately
Proper training is essential for safe operation of lifting equipment. Ensure that employees are competent, conversant with safety protocols, and understood the risks involved. Refresher training should be scheduled periodically.
6. Develop and Enforce Safety Procedures
Create comprehensive safety protocols aligned with LOLER requirements. Regularly review and update these procedures to incorporate new safety practices or equipment modifications.
7. Engage Competent Professionals
Partner with qualified inspectors and safety consultants who specialize in LOLER legislation. Their expertise ensures thorough examinations and accurate compliance assessment.
The Role of SafePlant UK in Supporting LOLER legislation Compliance
At safeplantuk.co.uk, we specialize in providing comprehensive services geared toward ensuring your business meets all aspects of LOLER legislation. Our solutions include:
- Professional inspection and certification of lifting equipment.
- Provision of reliable lifting and safety equipment tailored to your industry needs.
- Customized training programs for your staff to operate lifting gear safely and efficiently.
- Ongoing safety audits and compliance management support.
Partnering with experts like us helps you mitigate risks, avoid penalties, and foster a culture of safety in your business operations.
Benefits of Ensuring LOLER Legislation Compliance
Complying with LOLER legislation yields strategic advantages, including:
- Enhanced safety culture protecting employees and clients.
- Operational efficiency through well-maintained, reliable equipment.
- Reduced liability by minimizing the risk of accidents and legal repercussions.
- Improved reputation as a responsible and safety-conscious business.
- Cost savings by preventing costly repairs and downtime due to neglected equipment.
Stay Ahead of the Curve: Future Trends and Updates in LOLER Legislation
Legislation in safety standards continually evolves to meet emerging risks and technological advancements. Businesses must stay vigilant through:
- Regularly reviewing updates issued by the HSE or industry regulators.
- Participating in safety training and seminars focused on compliance.
- Incorporating new inspection technologies and safety management software.
- Engaging with expert consultants to adapt procedures proactively.
Proactive compliance ensures your business remains within legal boundaries and upholds the highest safety standards.
Conclusion: Embracing Safety Through LOLER Legislation
In conclusion, understanding and implementing LOLER legislation is an integral part of responsible business management within the Home & Garden, Gardeners, and Pest Control sectors. It not only safeguards your staff and clients but also enhances your operational credibility and financial stability.
Partner with experienced professionals like Safe Plant UK to ensure comprehensive compliance, cutting-edge safety solutions, and ongoing support. By prioritizing safety and regulatory adherence, your business can thrive in a competitive marketplace while maintaining the highest standards of responsibility and care.